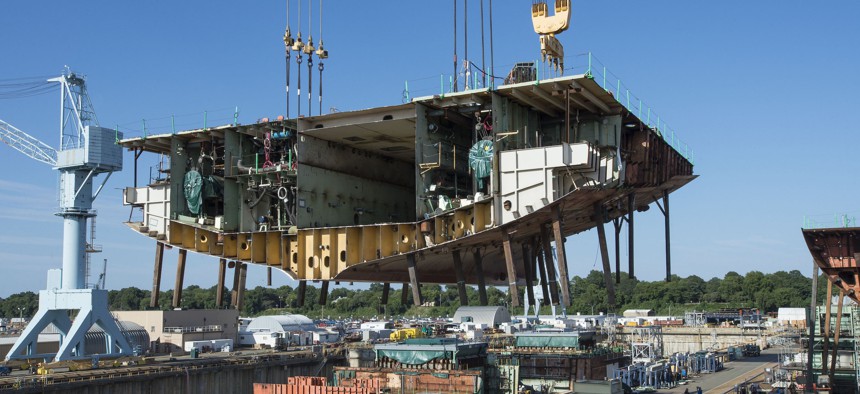
Newport News Shipbuilders lifted a 704-metric-ton aunit into Dry Dock 12, where construction of the aircraft carrier USS John F. Kennedy (CVN-79) is taking shape. Chris Oxley, Huntington Ingalls Industries
Robots and Lasers Are Bringing Shipbuilding into the Digital Age
Even decades-old aircraft carriers are being mapped onto digital models at Newport News Shipbuilding.
NEWPORT NEWS, Va. — When the USS George Washington took shape here in the late 1980s, endless paper blueprints guided the welders and shipfitters of Newport News Shipbuilding. Now, with the aircraft carrier back in a drydock for its midlife overhaul, shipyard workers are laser-scanning its spaces and bulkheads.
They’re compiling a digital model of the 104,000-ton carrier, which will allow subsequent Nimitz-class projects to be designed and planned on computers. That will help bring the shipyard’s carrier-overhaul work in line with its digital design-and-manufacturing processes that are already speeding up construction and maintenance on newer vessels.
Newport News executives say these digital shipbuilding concepts are revolutionizing the way ships are designed and built.
“We want to leverage technology, learn by doing and really drive it to the deckplates,” Chris Miner, vice president of in-service carriers, said during a tour of the shipyard. This is the future. This isn’t about if. This is where we need to go.”
This storied shipyard, now a division of Huntington Ingalls Industries, has been building warships for the U.S. Navy for more than 120 years. Some of its buildings are nearly that old, and some of its employees are fifth-generation shipbuilders. But the technology they use to design, build, and overhaul submarines and mammoth aircraft carriers is rapidly changing. Paper schematics are quickly becoming a thing of the past, being replaced by digital blueprints easily accessible to employees on handheld tablets.
“The new shipbuilders coming in, they’re not looking for you to hand them a 30-page or a 200-page drawing,” Miner said. “We’re really transitioning how we train folks and how we do things as far as getting them proficient.”
This digital data will “transform the business,” said Miner.
The technology is spreading beyond the shipbuilding sector. Boeing used digital tools to design a new pilot training jet for the Air Force and an aerial refueling drone from the Navy. The Air Force is planning to evaluate new engines for its B-52 bombers, nearly six-decade-old planes, using digital tools. The technology is allowing companies to build weapons faster than traditional manufacturing techniques.
Engineers here at Newport News Shipbuilding are already using digital blueprints to design ships, but they plan to expand the use of the technology into manufacturing in the coming years.
“We want to be able to leverage off all that data and use it,” Miner said. “There’s lots of things we can do with that [data].”
The USS Gerald Ford — the Navy’s newest aircraft carrier and first in its class — was designed using digital data. The Navy’s new Columbia-class nuclear submarines are being digitally designed as well.
Parts for the future USS Enterprise (CVN 80) — the third Ford-class carrier — are being built digitally. Data from the ship’s computerized blueprints are being fed into machines that fabricate parts.
“We’re seeing over 20 percent improvement in performance,” Miner said.
When the Navy announced it would buy two aircraft carriers at the same time, something not done since the 1980s, James Geurts, the head Navy acquisition, said digital design would contribute to “about an 82 percent learning from CVN79 through to CVN 81” — the second through fourth Ford ships. Geurts called the savings “a pretty remarkable accomplishment for the team.”
In the future, even more of that data will be pumped directly into the manufacturing robots that cut and weld more and more of a ship’s steel parts.
“That’s the future,” Miner said. “No drawings. They get a tablet. They can visualize it. They can manipulate it, see what it looks like before they even build it.”
As shipyard workers here give the George Washington a thorough working-over, they are using laser scanners to create digital blueprints of the ship. These digital blueprints are creating a more efficient workforce and reducing cutting as many as six months from a three-year overhaul, Miner said.
The top of its massive island — where sailors drive the ship and control aircraft — has been sliced off. It will be rebuilt in the coming months with a new design that will give the crew a better view of the flight deck.
The island already sports a new, sturdier mast that can hold larger antennas and sensors. Shipyard workers lowered it into place in early March.
The yard is also combining its digital ship designs with augmented reality gear to allow its designers and production crews to virtually “walk through” the Ford class’s spaces. This helped the yard figure out, for example, whether the ship’s sections were designed efficiently for maintenance.
In addition to robots, the additive manufacturing techniques, like 3D printing, could speed shipbuilding even more and reduce the Navy’s need for carrying spare parts on ships. The Navy is testing a valve 3D-printed here.
Right now, at a time when the Navy is planning to drastically expand its fleet size, shipyards like Newport News are expanding, but not yet to the levels of the Reagan military buildup of the 1980s. Despite the technology advantages, Miner said people still play essential roles in the manufacturing process.
“It’s really not about reducing our workforce as much it is about doing more with the workforce we have,” he said. “We’re still going to hire people. We still have to ramp up. There’s still hands-on things that are always going to have to be done. But it definitely helps us with cycle time to be able to build things quicker" and "enable our workforce to be more efficient.”