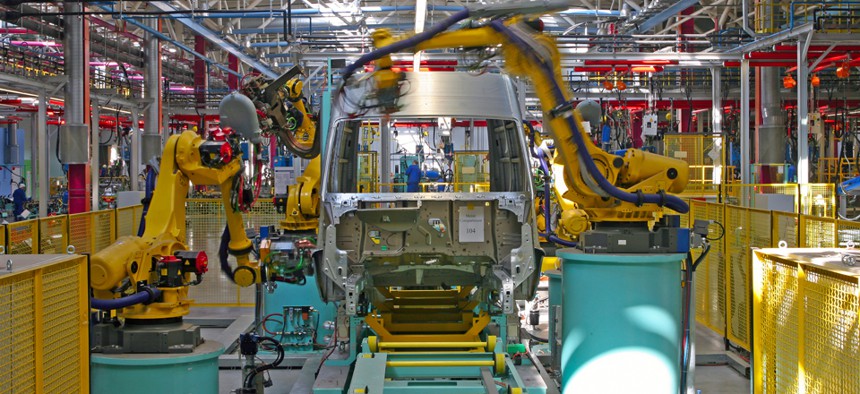
vladimir salman/Shutterstock.com
Shaping the Workforce You Need: Lessons From a Manufacturing Innovator
How Shinola turned janitors, manicurists, and autoworkers into fine watchmakers.
Shinola, a watch and leather goods maker, has done the impossible in its Detroit factory: cracked the code on how to skill up workers.
Willie Holley is one of them. He used to be a security guard for the company. Two years ago, he asked if he could try making watches and underwent a rigorous training program that teaches the obscure art of fine-watch assembly. Now, two years later, he’s a line leader, managing other watchmakers, and gets full benefits and a higher salary.
As the US crawls out of a jobless recovery, it seems unbelievable that manufacturing companies claim they can’t fill jobs. But according to the 2014 ManpowerGroup survey, firms who employ manufacturing occupations report the biggest shortage of talent; according to a 2011 study by Deloitte, 5%n of manufacturing jobs go unfilled due to a shortage of appropriate skills.
The manufacturing industry in America now employs fewer people, but it’s still an important source of middle class jobs. In 1970, nearly a quarter of Americans worked in manufacturing—now only about 10% do. This isn’t a trend limited to America; it is in large part, due to technology. Manufacturing work now requires fewer hands, but even as the industry shrinks it can’t find people with the right skills to fill jobs at a price they can pay.
That’s because once upon a time, manufacturing jobs entailed more routine tasks. An auto assembly plan, traditionally a big employer in Detroit, could take someone with a high school diploma, train him fairly quickly, and provide him with a comfortable, benefit rich, middle-class life assembling cars. But now that’s less common. According to Kim Hill of the Center for Automotive Research, when it comes to auto assembly: “Certainly the jobs are more technical than they were 30 years ago, or even 10 years ago. In order to work on an assembly line, prospective employees must have an associate’s degree—or equivalent—before they are even considered for employment.”
This change in the manufacturing industry has polarized the economy. Jobs that pay a middle-class wage, which manufacturing used to provide, have been disappearing and replaced by either low-skill, low pay or high skilled, high pay jobs. This trend has been going on for decades and accelerated during the recession. And it makes vacant manufacturing jobs all the more frustrating.
The solution from the government and most employers is more education, the type of training available at community colleges or vocational high schools. But so far, the results haven’t been great. Manufacturers still have unfilled jobs and less than 20% of enrollees at many community colleges graduate within three years. We still don’t know how and where training can be done successfully and who should pay for it.
This is precisely why what Shinola has done is so remarkable. It took people with diverse backgrounds (employees’ previous jobs also include janitors, pizza delivery, manicurists, and autoworkers) and transformed them into fine watchmakers, a skill only gained through an intense, long apprenticeship with Swiss master craftspeople. The process started about two years ago when the factory opened with a mission to make top quality watches in Detroit. The founder, Tom Kartsotis,had already found success with watch making, from an earlier company he started, Fossil.
According to Shinola CEO Steve Bock, the key to training success was partnering with Swiss company Ronda. Ronda supplies most of the parts (assembly occurs in the Detroit factory) and provided training in the art of watch assembly. Bock credits the Ronda partnership since, while fine watchmaking can be taught, few people know how to do it well enough to train others. The skills are traditional passed down through years-long, intensive apprenticeships in Switzerland.
Bock estimates Shinola has successfully trained between 75 and 80 workers. But it took time and money. To be successful, workers must deliver consistent quality and be efficient. He explained, “You can assemble a watch after a few weeks, but achieving acceptable speed and quality takes time. We now feel confident enough to provide a lifetime guarantee and meet demand—we couldn’t the first year. “ It was more than a year before Shinola could make enough watches of acceptable quality to meet demand.
Shinola is selective about employment, accepting only about 20% of applicants. The primary and most discriminating attribute required is the physical dexterity necessary for watch assembly. Part of the interview process is a 10-step dexterity test, which determines if prospective employees have the innate physical ability to do the work. The test involves performing several intricate timed tasks using tweezers.
And so Shinola has managed to train a skilled staff, the Holy Grail in modern manufacturing. But is in-house training always the best approach and is it scalable? Other small manufacturers would struggle to carry the cost of a non-profitable worker for a year and employ master craftsmen to lead training. Also watchmaking is fairly specialized. Shinola needn’t worry that their workers will take their valuable skills to a competitor because companies using a similar technology are largely in Switzerland.
Poaching may be a problem at other firms though. For instance, Hill points out that auto manufacturing may require more skills, but it also has become more standardized. “Once you have this knowledge (and experience), it is relatively easy to move from one employer to another—such as moving from Magna to JCI, or Ford to Toyota.”
That may be why the more popular alternative is to train people at community colleges. This puts the cost of training on the prospective employee or the government, through grants and subsidies, instead of the employer. But being trained in a classroom, and not the factory, introduces the risk that the wrong skills are taught. Also, according to Simon McDonnell of the CUNY (the community college network in New York City) Office of Policy Research, the right curriculum is necessary, but not sufficient. He explained, “Training most for technical jobs require a basic math foundation and often calculus, and many of the students don’t have that.”
After many students enroll they have to be placed in remedial math classes and then they often get frustrated and drop out.” Remedial math classes are sometimes called the “killing fields” because of the high drop out rate they induce. Calculus may not be necessary for watchmaking, but it is for many manufacturing jobs.
McDonnell also says financing is important; many students drop out when they lose funding. The fact that Shinola employees get a paycheck, a supportive work environment, and a clear career path, probably accounts for low turnover in the last two years, even as workers experience a long, and frustrating, training period.
Figuring out how to transform a large part of the population into skilled workers is necessary to preserve much of the middle class. There is no shortage of people who want these skills and are willing to work hard for them. We can see from Shinola’s experience it is possible, but successful training is labor intensive, requires highly skilled people to do the training, and can be expensive.
Closer partnerships between factories and colleges will ensure the right skills are taught and the costs are evenly shared among everyone who benefits: employers, employees, and tax-payers. The future of the middle class is counting on it.
(Image via vladimir salman/Shutterstock.com)