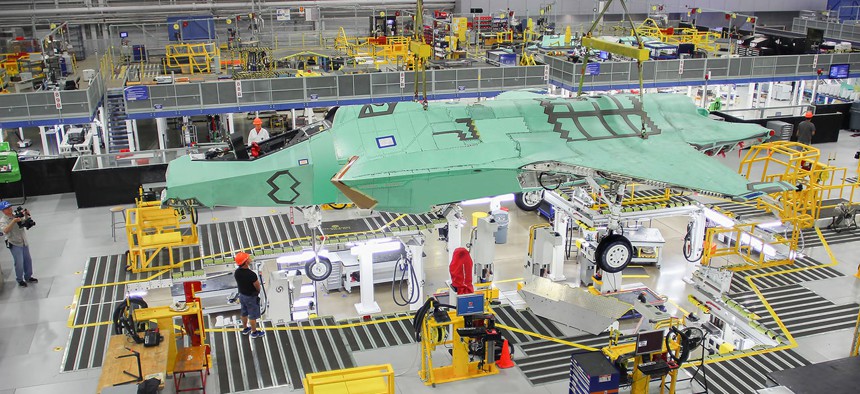
Norway's first F-35 is lifted by an overhead crane in Lockheed Martin's assembly plant in Fort Worth in April 2015. Lockheed Martin
F-35 Production Set to Quadruple As Factory Retools
After years of delays, the Joint Strike Fighter program is finally ready to hit the afterburner.
FORT WORTH, Texas — As green-skinned, half-assembled F-35 Joint Strike Fighters take shape, this massive factory that once cranked out thousands of World War II bombers is preparing to get real busy again.
F-35 production is slated to hit full steam in 2019, and Lockheed Martin is reshaping its final assembly line to get ready. Not far from the nine assembly stations where the stealthy jets are coming together, wooden walls and plastic sheeting rise dozens of feet to the ceiling, blocking off large portions of the plant where new laser-leveled concrete is being poured. Lowered air pressure behind the screens helps keep dust and debris away from the sensitive airframes. Elsewhere, scaffolding is being erected for seven new assembly stations to come.
“I came to work here eight years ago,” said Lockheed spokesman Mike Rein. “Nothing in this building right here, apart from the walls and the ceiling, looks the same.”
For all of the F-35’s early developmental troubles and the various bugs still being squashed, production of the stealthy jet has been slowly rising since the first one flew in 2006. Earlier plans called for full production by now, but that was delayed by problems that ultimately added billions of dollars to the cost. But now, production is poised to explode. This year, Lockheed will build 53 F-35s here and at another assembly facility in Italy, pushing the worldwide total past 200. That’s more than the Air Force has F-22 Raptors.
By 2020, one year after the Fort Worth plant hits its full 17-jet-per-month stride, there will be more than 600 F-35s, including nearly 180 sent to U.S. allies.
Most will be assembled by Lockheed, the world’s largest defense contractor, in this mile-long building formally known as Air Force Plant 4. More than 10,000 planes have been born here, including the B-24 Liberator, B-36 Peacemaker, F-111 Aardvark, and F-16 Fighting Falcon. The F-35 is expected to add nearly three thousand to that total: nearly 2,500 for the U.S. military and hundreds more for allies.
While the exterior hasn’t changed much — Plant 4 has historic status — its insides would be unrecognizable to Rosie the Riveter. As turboprops gave way to jets and aluminum skins to carbon-fiber composite, the plant and its floor have evolved. Today, the plant’s guts are changing again as it prepares to close out more than four decades of F-16 production.
“Everything inside, we can modernize,” Kevin McCormick, an employee of 30-plus years, said during a tour of the plant earlier this week.
The F-35 is a complicated construction of 300,000 parts from 1,100-plus suppliers whose sprawling supply chain touches nearly every U.S. state and countries around the world. But final assembly is largely a matter of connecting three fuselage sections plus wings.
“Those four major components come together right here,” McCormick said.
Plant 4 does the major assembly on the forward fuselage and wings. One quarter-mile stretch of factory floor is dedicated to making the wings. Every five days, pieces of wing move from one station to the next. Later this year, that interval will be cut to four.
Other key sections are assembled elsewhere, and arrive here in big chunks. Center fuselages are made by Northrop Grumman in Palmdale, California, and by Turkish Aerospace Industries in Ankara, Turkey. The aft section is made by BAE Systems in the U.K.
In all, foreign suppliers make about half of each F-35. Increasingly, they are doing final assembly as well. Lockheed has replicated the Fort Worth plant in Italy, where Alenia Aermacchi finished its first jet last year and could build F-35s for other European allies, and in Japan, which is supposed to finish assembling its first plane next year.
There’s already an international feel in Fort Worth. On Tuesday morning, a ceiling crane hoisted the center section of an Israeli jet from one assembly station to the next. Nearby, a robot drilled precise, laser-guided holes into the green wings of Norway’s eighth F-35. Farther south, Japan’s first F-35A and the U.K. Royal Air Force’s seventh F-35B slowly meandered their way northward. Simple printed cards in plastic sheets marked the Air Force’s 104th jet and the U.S. Marine Corps’ 55th F-35B.
That latter plane awaited its Pratt & Whitney engine and Rolls-Royce lift fan. Its outer panels had yet to arrive, exposing some of its 16 miles of cables and the white boxes that feed the jet’s cognitive electronic warfare suite. In a few weeks, it would be the 225th Joint Strike Fighter to roll off the line.
Remarkably Quiet
Despite its vast size, the plant is remarkably quiet. There is no riveting or hammering. The occasional warning buzzer sounds when parts of the jets are moved down the assembly line. Parts and tools are shuttled around on golf-cart-sized vehicles; employees ride bicycles because it’s faster than walking. To keep the tools properly calibrated, the temperature inside is always 72 degrees Fahrenheit.
All three F-35 variants are produced on this line, and by the same workers. The variants share only about 30 percent of their parts; the rest are variant-specific. For example, the wing on the Navy’s F-35, built to handle aircraft-carrier operations, is 40 percent larger than the wing on the Air Force’s conventional F-35A and the Marines’ vertical-landing F-35B. To accommodate the different wing sizes, special slats in the scaffolding slide in and out to fill in the gaps.
More than 2,200 people work on the assembly line, supported by another 1,500 office workers nearby. When production reaches full steam, larger around-the-clock shifts are expected.
The amount of time it takes to build a jet has come down steadily, said Eric Van Camp, Lockheed's director of F-35 business development. It took about 160,000 labor hours to build the first F-35A in 2006. (The first F-35B took about 140,000 hours and the first F-35C took 130,000 hours.) But the most recent F-35A required only about 43,000 hours.
“There’s common learning that goes on between the variants,” Van Camp said.
And even as they prepare for full F-35 production, Lockheed and its partners are eyeing new manufacturing techniques that they hope could trim $10 million from each plane’s price tag, bringing it to $80 million by 2019. (The Pentagon says each one currently costs $100 million.) Collectively, Lockheed, Northrop and BAE have invested $132 million to help reduce the cost of the planes, Rein said.
For example, Lockheed is experimenting with a new way to drill the F-35’s wings. Currently, water and oil are used to cool a robotic drill bit so it doesn’t overheat and break. It’s a messy process, with fluid dripping down each wing. The new way uses cryogenic machining — essentially, freezing the drill bit beforehand instead of cooling it as it goes, Rein said. The company spent $119,000 testing the process, which it says will save $400,000 per jet, saving $12 million over the life of the program.
Another $298,000 investment in new forging techniques on the F-35C has trimmed about $30,000 per jet, totalling $10 million over the life of the program. It might not seem like much money, but with the total program expected to cost $379 billion, any savings matter.
At the north end of the factory, the Air Force’s 100th F-35 waited to make the short trip to an adjacent building, where a robotic arm will spray it with special stealth paint. After the stop at the paint shop — which itself is about to expand to keep up with the increased production — the plane will make a few flight tests before heading to Luke Air Force Base in Arizona.
The forward section of that Air Force jet was made in America, the center in Turkey, the wings in Italy and the aft end in the U.K.
“That’s the first time that configuration has come together,” McCormick said.
NEXT STORY: Why Most Training Doesn't Work